What is Turbulent Flow?
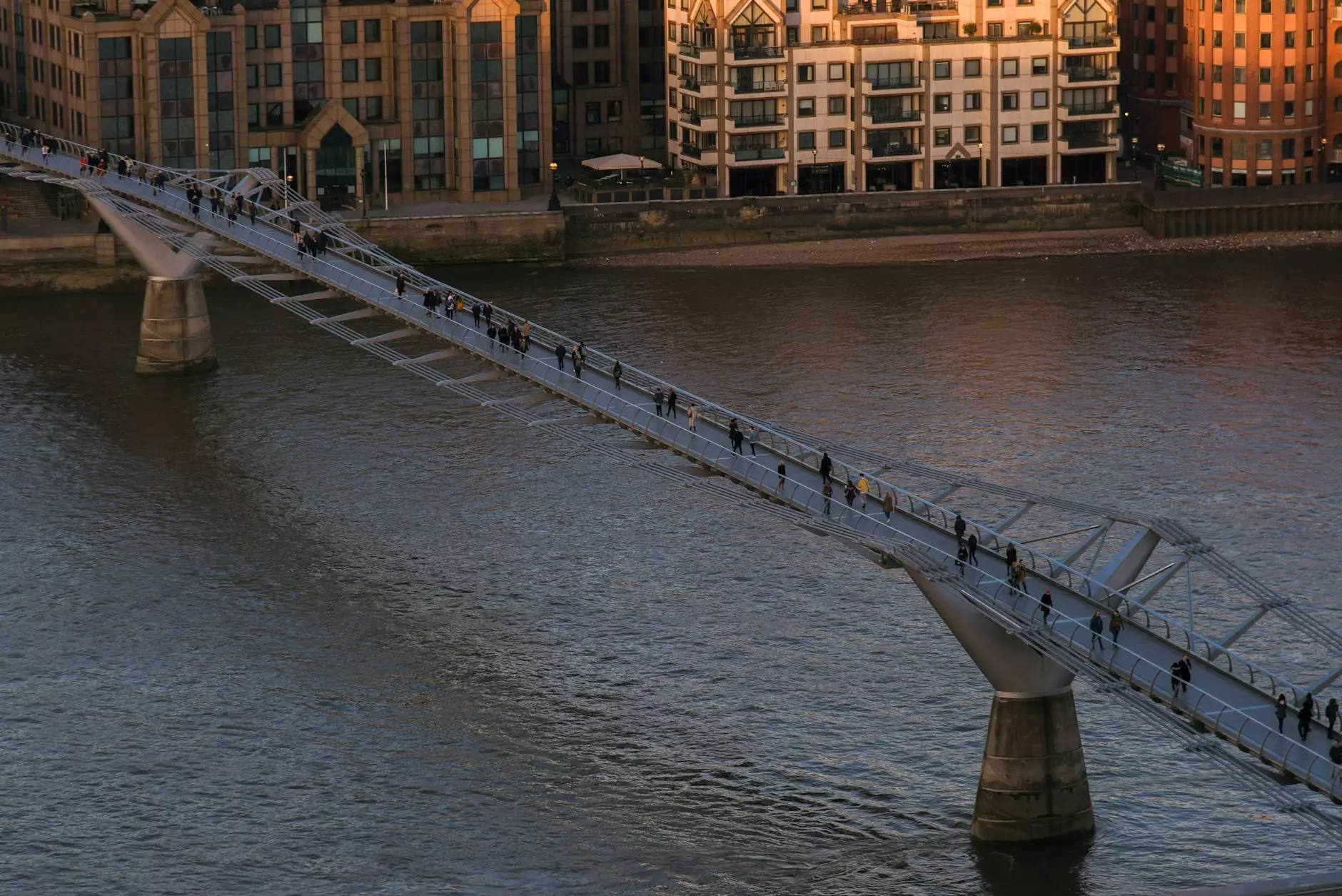
Turbulent flow is a complex and fascinating phenomenon in fluid dynamics characterized by chaotic property changes, including rapid velocity fluctuations and swirling eddies. In a turbulent flow, fluid particles follow irregular paths, leading to increased mixing and energy dissipation. Understanding turbulent flow is crucial for various engineering applications, particularly in sectors such as auto repair, farm equipment repair, and structural engineering.
The Nature of Turbulent Flow
To grasp the concept of turbulent flow, it's essential to contrast it with its counterpart, laminar flow. In laminar flow, fluid moves in parallel layers, with minimal disruption between them. This occurs at lower velocities and is influenced by factors such as fluid viscosity and flow geometry.
In turbulent flow, the Reynolds number—a dimensionless quantity used to predict flow patterns in different fluid flow situations—plays a significant role. When the Reynolds number exceeds 4000 for flow in a pipe, the flow is typically classified as turbulent. This transition leads to various implications in engineering and design.
Key Characteristics of Turbulent Flow
- Irregular Fluctuations: Turbulent flows exhibit random fluctuations in velocity and pressure.
- Increased Mixing: Turbulent flow enhances the mixing of fluid layers, which is beneficial in processes such as combustion in engines.
- Energy Loss: The chaotic nature of turbulent flow often leads to increased friction and energy loss, a critical factor in engineering design.
- Enhanced Heat Transfer: Turbulent flows can improve heat transfer rates, making them advantageous in thermal systems.
Importance of Turbulent Flow in Engineering
The understanding of turbulent flow is indispensable across various engineering domains. Below, we explore its significance in three key categories relevant to companies like Michael Smith Engineers.
1. Auto Repair and Turbulent Flow
In the automotive industry, the principles of turbulent flow are crucial for optimizing engine performance. For example:
- Fuel Injection: Modern engines utilize fuel injectors to create a turbulent mix of fuel and air, enhancing combustion efficiency.
- Exhaust Systems: Understanding turbulent flow helps in designing exhaust systems that improve the discharge of gases, reducing back pressure and improving performance.
- Cooling Systems: Turbulent flow in cooling systems helps to maintain optimal temperatures, ensuring engine longevity and performance.
2. Farm Equipment Repair and Turbulent Flow
In agriculture, where machinery operates in diverse conditions, turbulent flow principles apply in several ways:
- Irrigation Systems: Achieving uniform water distribution in irrigation systems often requires understanding turbulent water flow in pipes.
- Fuel Efficiency: Enhancing the combustion process in farm machinery contributes to better fuel efficiency, which is directly influenced by how well the fuel and air mix.
- Hydraulic Systems: Turbulent flow is critical in designing hydraulic systems that operate effectively under varying pressures and conditions.
3. Structural Engineering and Turbulent Flow
Structural engineers must also consider the effects of turbulent flow in their designs:
- Aerodynamics: Understanding how wind interacts with structures can prevent potential damage caused by turbulent airflows.
- Water Flow Management: For structures built near water bodies, it’s crucial to understand how turbulent water flow can affect foundations and erosion.
- HVAC Systems: The efficiency of heating, ventilation, and air conditioning systems (HVAC) is enhanced through the principles of turbulent flow, impacting indoor air quality.
The Science Behind Turbulent Flow
The transition to turbulent flow can be described using several fluid dynamics principles. Key aspects include:
1. The Reynolds Number
The Reynolds number (Re) serves as a criterion for predicting flow regimes. It is calculated using the formula:
Re = (ρ * v * L) / μ
Where:
- ρ = fluid density
- v = mean velocity of the fluid
- L = characteristic length (like diameter of a pipe)
- μ = dynamic viscosity of the fluid
Hence, the transition from laminar to turbulent flow typically occurs when Re exceeds 4000. Understanding this transition aids engineers in designing systems that handle fluid dynamics more effectively.
2. Flow Visualization Techniques
Engineers utilize various techniques to visualize and analyze turbulent flows, such as:
- Particle Image Velocimetry (PIV): A technique that uses laser illumination and digital imaging to measure flow velocities.
- Smoke Flow Visualization: Injecting smoke into a flow allows engineers to see the movement of fluid and identify laminar and turbulent regions.
- Computational Fluid Dynamics (CFD): Software solutions that simulate fluid flow to predict behavior and observe the effects of design changes.
Challenges and Considerations in Managing Turbulent Flow
Despite its advantages, turbulent flow can present challenges in various engineering applications:
1. Flow Control
In many engineering systems, controlling turbulent flow can enhance performance. Techniques include:
- Incorporating Flow Straighteners: These devices can help reduce turbulence by straightening fluid pathways.
- Surface Modifications: Changing the surface roughness of pipes can influence turbulence characteristics.
- Active Flow Control: Innovative methods, such as using oscillating surfaces, can actively manage turbulent conditions.
2. Energy Efficiency
Managing the energy losses associated with turbulent flow is essential:
- Optimizing Pipe Design: Engineers can design pipes with the right diameter and surface finish to minimize turbulence-induced losses.
- Using Advanced Materials: Employing materials that reduce friction can significantly lower energy consumption in fluid transport systems.
Future Trends in Understanding Turbulent Flow
As technology advances, the study of turbulent flow continues to grow. Key trends include:
1. Enhanced Computational Models
With the increasing capability of computational power, engineers are developing more sophisticated Computational Fluid Dynamics (CFD) models. These models help bridge the gap between theoretical predictions and real-world applications, contributing to better design outcomes.
2. Experimentation with New Materials
Innovative materials that are smooth and low-friction can significantly alter the behavior of turbulent flow. Research into coatings and composites will further enhance efficiency in engineering applications.
Conclusion
In conclusion, understanding what turbulent flow is, its characteristics, and implications is vital for engineers across different fields. From enhancing the efficiency of auto repair processes to optimizing systems in farm equipment repair and structural engineering, knowledge of turbulent flow significantly impacts operational effectiveness and innovation.
As industries continue to evolve, embracing the complexities of turbulent flow will help engineers design smarter, more efficient systems that meet modern challenges effectively.
what is turbulent flow