The Future of Manufacturing: Exploring the World of Injection Molding Makers
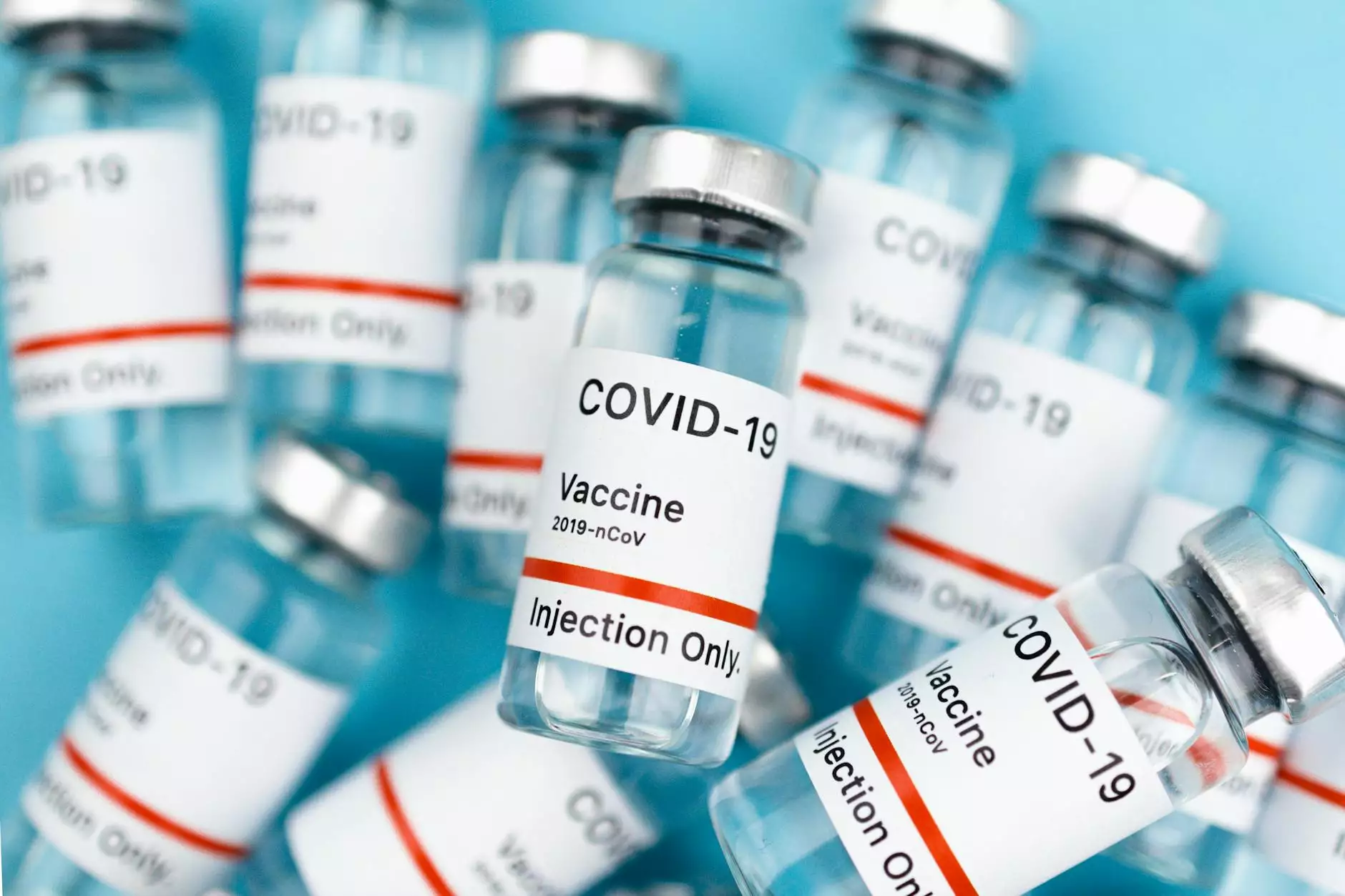
In today's fast-paced industrial environment, injection molding has become a cornerstone for manufacturers seeking efficiency, precision, and quality in their production processes. Selecting the right injection molding maker can significantly influence product quality, lowering production costs and enhancing time-to-market. Let's delve deeper into what makes an injection molding maker stand out and how they can propel your business to the next level.
What is Injection Molding?
Injection molding is a manufacturing process used for producing parts by injecting molten material into a mold. The most common materials used are thermoplastics and thermosetting polymers. Here’s a quick overview of the process:
- Material Selection: Choosing the appropriate plastic material based on the application.
- Heating: The material is heated until it becomes molten.
- Injection: The molten plastic is injected into a mold cavity.
- Cooling: The material cools and hardens into the final product shape.
- Demolding: The mold is opened and the finished part is removed.
Benefits of Injection Molding
Understanding the benefits of injection molding is crucial for businesses weighing their manufacturing options. Here are some key advantages:
- High Efficiency: The injection molding process allows for rapid production, making it ideal for large quantities.
- Cost-Effective: Once the molds are made, the cost of producing each additional part is minimal.
- Precision and Accuracy: Injection molding creates highly detailed parts with tight tolerances.
- Versatility: A wide variety of materials can be used, including different types of plastics, metals, and even composites.
- Reduced Waste: The process produces minimal waste compared to other manufacturing methods.
Finding the Right Injection Molding Maker
Choosing the right injection molding maker is vital for ensuring your projects are completed on time and within budget. Here are several factors to consider:
1. Expertise and Experience
When evaluating an injection molding maker, assess their experience in the industry. An experienced maker will understand the nuances of different materials, processes, and design considerations. Look for makers who have completed projects similar to yours, as their insights can be invaluable.
2. Quality of Machinery
The machinery used in the injection molding process greatly affects the quality of the output. Ensure that the injection molding maker uses state-of-the-art, well-maintained equipment to produce parts with precision
. Advanced machinery not only improves quality but can also ramp up production speeds, leading to quicker turnaround times for your products.3. Design Capabilities
A proficient injection molding partner should have robust design capabilities. This includes experience with CAD software and the ability to offer prototyping services. They should work with you to optimize part designs for manufacturability, ensuring your product meets both functional and aesthetic requirements.
4. Material Knowledge
Different applications require different materials. The right injection molding maker should have an in-depth knowledge of various materials and their properties. This ensures that they can recommend the best material for your specific application, factoring in tolerances, environmental conditions, and end-use requirements.
5. Testing and Quality Assurance
Quality assurance is crucial in injection molding. Look for makers that incorporate rigorous testing and inspection protocols into their processes. This includes testing for dimensional stability, surface quality, and functional performance to ensure that every part meets the required specifications.
6. Sustainability Practices
As environmental concerns grow, more businesses are looking for sustainable practices in their supply chain. The ideal injection molding maker should implement eco-friendly practices, such as waste reduction methods, recycling programs, and energy-efficient machinery. This not only helps the environment but can also enhance your brand's image.
7. Client Testimonials and Case Studies
Client feedback is invaluable when assessing a potential injection molding maker. Look for testimonials and case studies highlighting their successes. Positive feedback from past clients can provide insight into the maker's reliability, quality, and customer service.
Injection Molding Processes and Techniques
Injection molding encompasses various techniques tailored to different product needs. Each technique has its unique advantages and applications:
1. Standard Injection Molding
The most commonly used method, standard injection molding is efficient for producing high-volume plastic parts. It works well for simple shapes and designs.
2. Insert Molding
This technique involves inserting metal or other materials into the mold before the plastic is injected. This is ideal for parts that require additional strength or components, integrating multiple materials in a single operation.
3. Overmolding
Overmolding enables manufacturers to combine two different materials into a single component, providing enhanced functionality, such as a soft grip area on a plastic tool. This is particularly useful in consumer products.
4. Multi-material Injection Molding
This innovative process allows for the creation of complex parts using multiple materials. It is beneficial for products that require varying material properties, such as flexibility and rigidity.
5. Gas-assisted Injection Molding
Gas-assisted injection molding uses gas to help fill the mold, often resulting in lighter parts with less material used. This technique allows for more complex designs and can aid in reducing cycle times.
Cost Factors in Injection Molding
Understanding the cost structure of injection molding is critical for budgeting your projects. Here are some primary factors that influence costs:
1. Tooling Costs
The most significant upfront cost in injection molding is the creation of molds. High-quality molds are essential for producing consistent parts, but they can be expensive to design and fabricate. However, the cost per part decreases significantly with larger production volumes.
2. Material Costs
Material choice can dramatically impact costs. Different types of plastics vary in price, and the selection of specialty materials may further increase expenses. Work closely with your injection molding maker to select materials that balance cost and performance.
3. Production Volume
The volume of parts you need influences pricing as well. Typically, higher volumes lead to lower costs per unit. However, smaller runs can still be economically feasible, especially for prototyping or small-scale production, depending on the contract style with your maker.
Future Trends in Injection Molding
The injection molding industry is continuously evolving, with emerging technologies reshaping production techniques. Here are a few trends to keep an eye on:
1. Automation and Robotics
Incorporating automation in injection molding helps improve efficiency and reduces the risk of human error. Automated systems can monitor processes in real-time, leading to better quality control and production consistency.
2. 3D Printing Integration
As 3D printing technology matures, integrating these capabilities with injection molding to create prototypes or even molds is becoming more common. This blend can shorten design cycles and enhance innovation.
3. Sustainability Initiatives
With increasing focus on environmental sustainability, injection molding makers are exploring bioplastics and recyclable materials. The industry is poised for growth in developing eco-friendly processes to cater to changing consumer demands.
4. Smart Manufacturing
The implementation of Industry 4.0 technologies, including IoT and AI, is paving the way for smarter manufacturing processes. These innovations can lead to enhanced decision-making and operational efficiency.
Conclusion
Choosing the right injection molding maker is pivotal for businesses aiming to achieve high-quality products efficiently and cost-effectively. By understanding the intricacies of injection molding, from its processes and benefits to the trends shaping its future, companies can position themselves for sustainable success. Investing time and resources in finding the right partner can lead to significant competitive advantages in today's manufacturing landscape.
As a leader in the metal fabrication industry, Deep Mould stands out by delivering exceptional injection molding services tailored to meet your needs. Whether you are large-scale manufacturing or require bespoke injection molded parts, our expertise and cutting-edge technology will ensure your projects meet the highest standards.